Your cart is empty
Keep ShoppingPractised throughout history, jade carving is a difficult task to master.
While modern tools have allowed more complex designs to be made and the art of crafting jade to become more efficient, carving today remains an intensely painstaking and exacting art form. Every piece crafted in our workshop is carved by hand, and finished by hand - there is no mass production. Our carvers appreciate the rarity and value of the stone they’re working, always taking extreme care not to waste any.
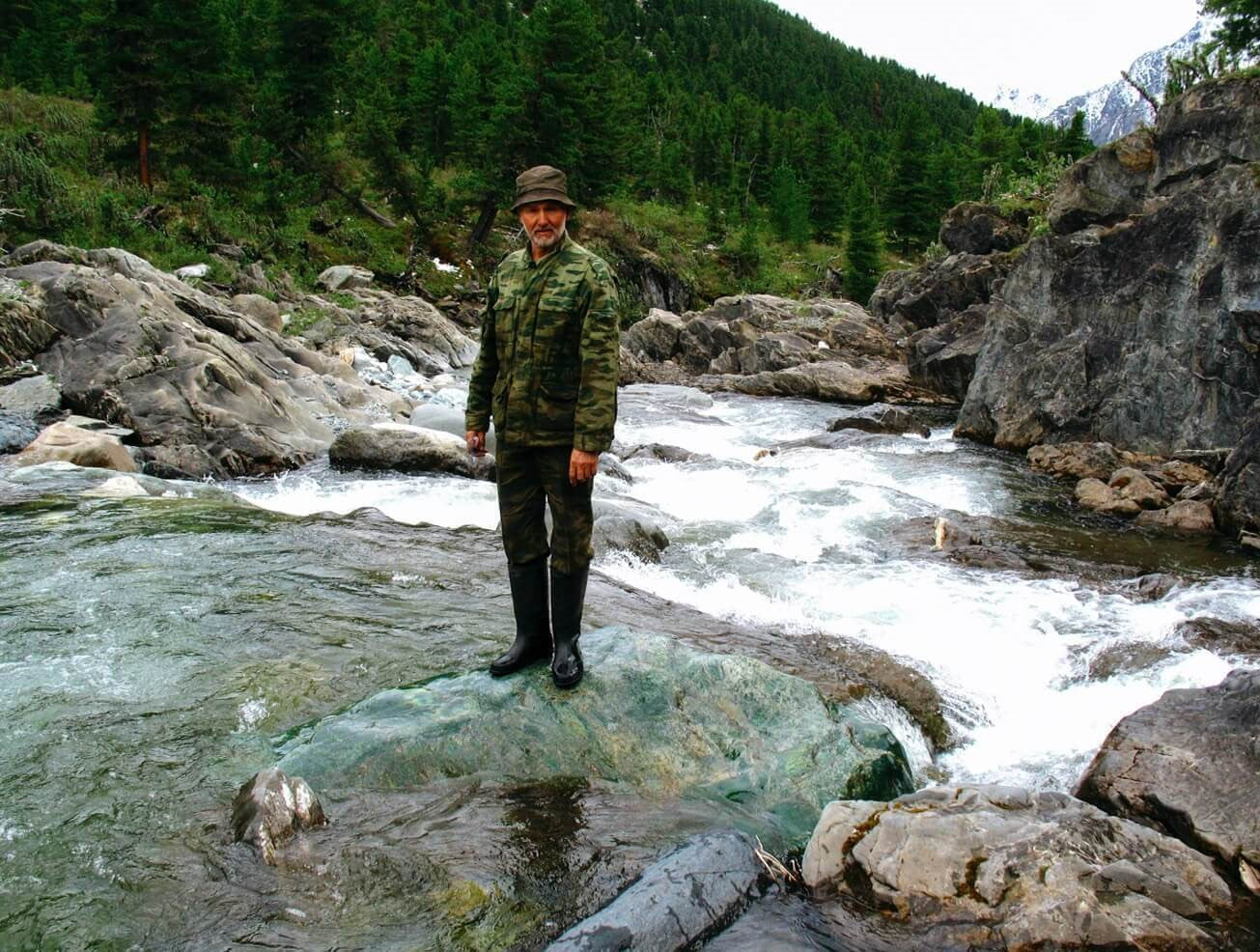
Seeking the stone
Sourcing jade is the first step in the carving process. Usually located in mountainous areas and rivers, jade can be difficult to distinguish from other rocks as oxidation leads to a brown or grey rind covering the surface of the stone. We've explored the world's sources of jade for over thirty years, searching out pieces that excite us. We make it our mission to actively source the finest quality jade, from every corner of the world - wherever it takes us.
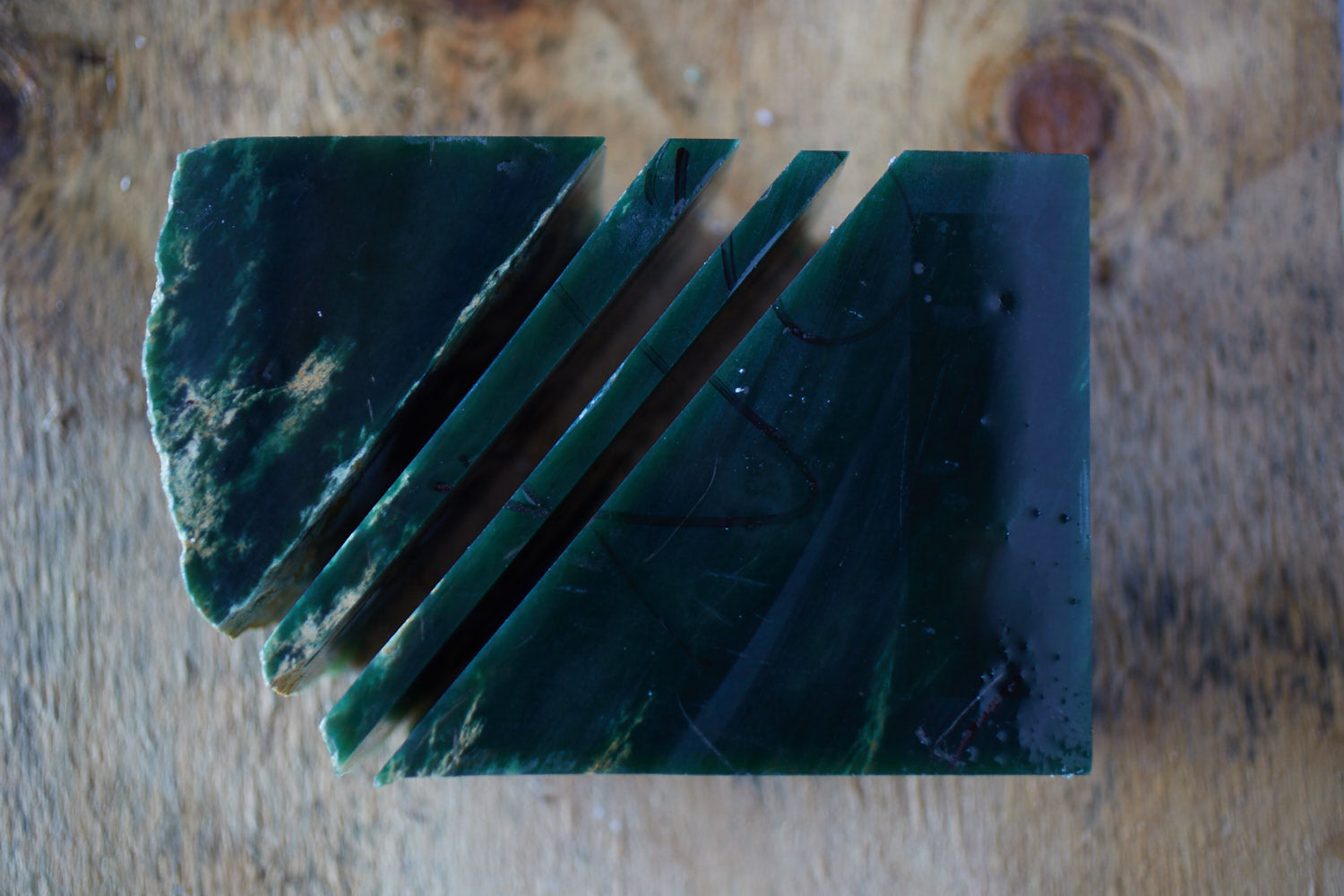
Slabbing and grading
Once extracted from the wilderness, an experienced carver will cut the tough stone into manageable sizes using a large diamond-tipped drop saw. Reading a stone is one of the most important skills a carver can have as jade has a grain, just like wood. To ensure the stone keeps its strength and integrity, a carver must take great care to cut along the grain - otherwise pieces of the material will splinter away. Once cut, each slab is given a different grade based on the quality of the stone and inspected for flaws and cracks.
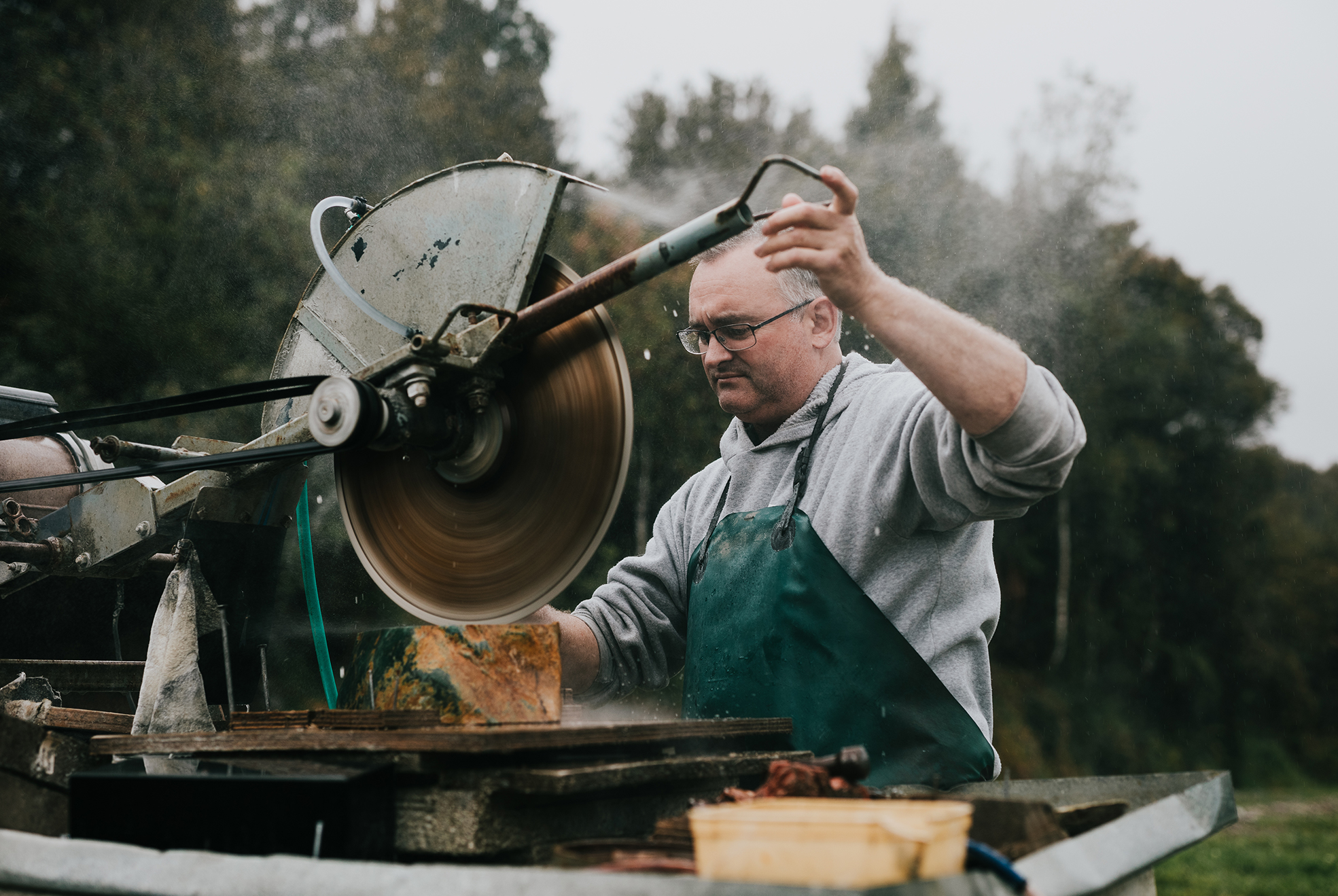
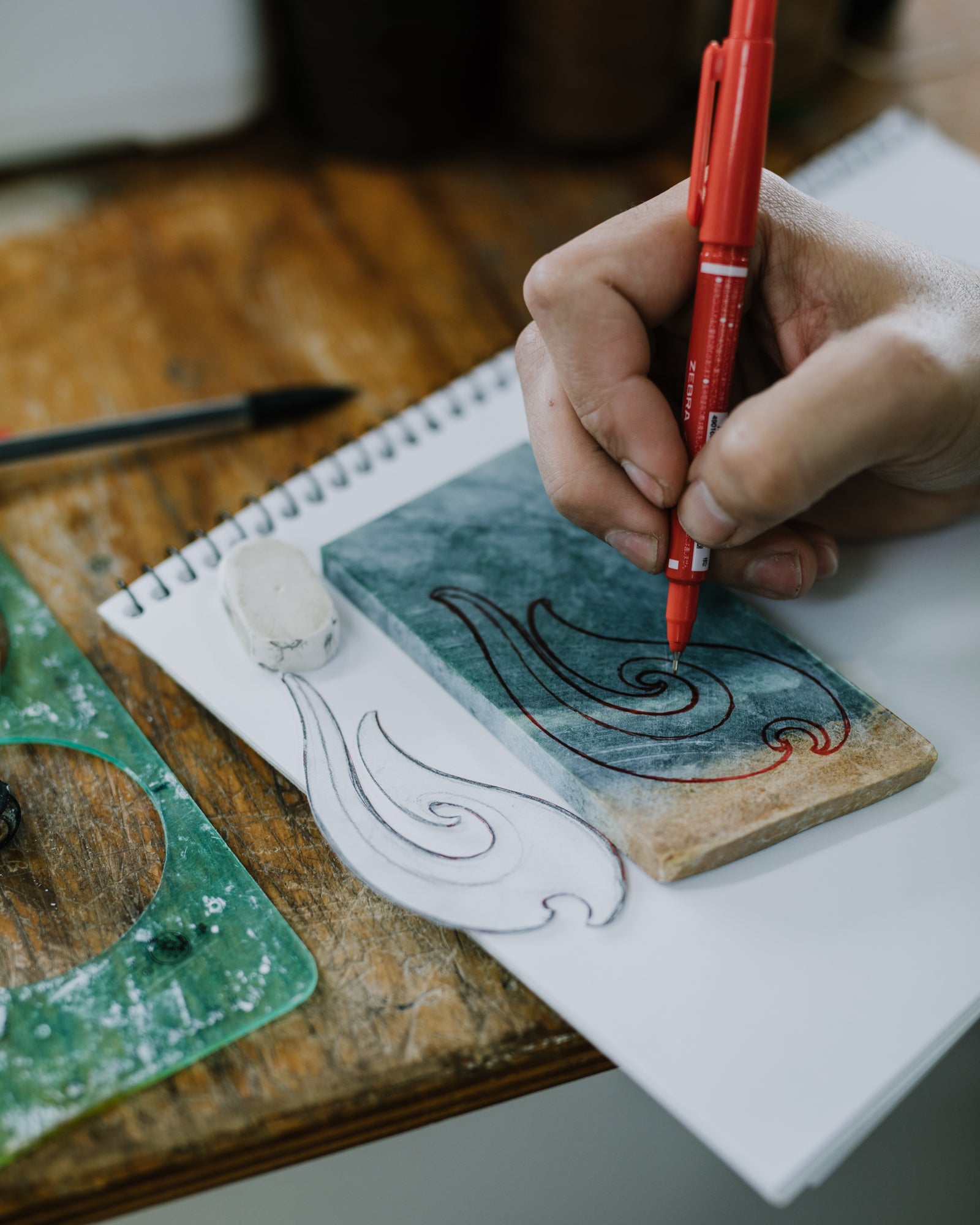
Elements of Designs
Each design is influenced by the raw material. An experienced carver will closely study a stone’s colour, clarity and patterning before the design process can begin. Once a template is sketched, the design is transferred onto the stone. Our carvers often edit their designs during this stage, to ensure they honour the jade by best utilising the stone - rather than trying to make the stone fit the design. Artists who progress beyond replica carving towards designing truly unique and progressive pieces of work must be able to sketch. This forms the foundation of an artist’s capabilities, yet it’s one part of the process that many carvers have yet to master.
Cutting
With the design in place, straight lines are drawn as close as possible to the sketch, creating a rough shape to be cut out with a diamond-tipped trim saw. The small off-cuts from the stone are used to make smaller pendants, earrings and bracelets, ensuring no jade is wasted.
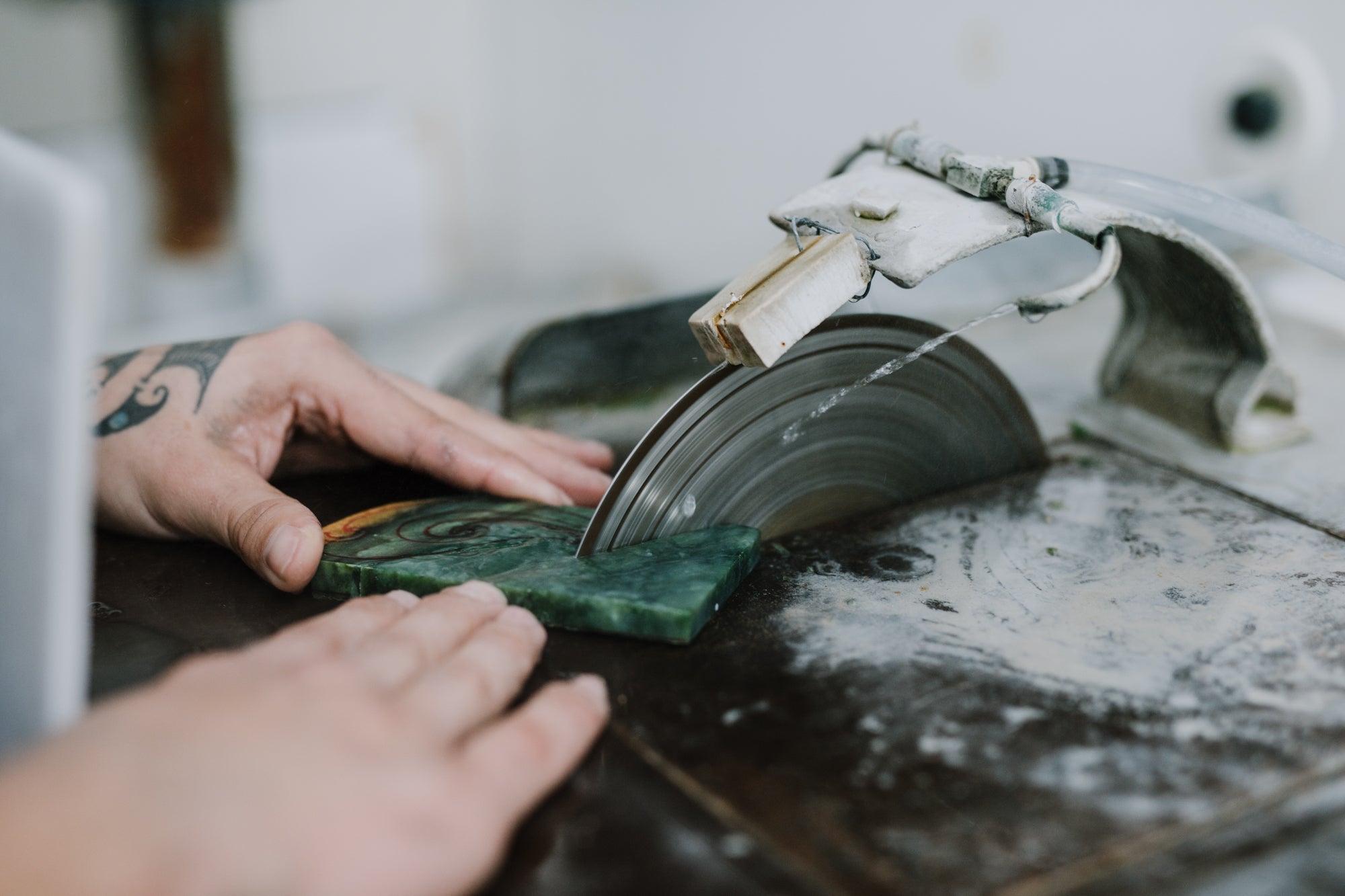
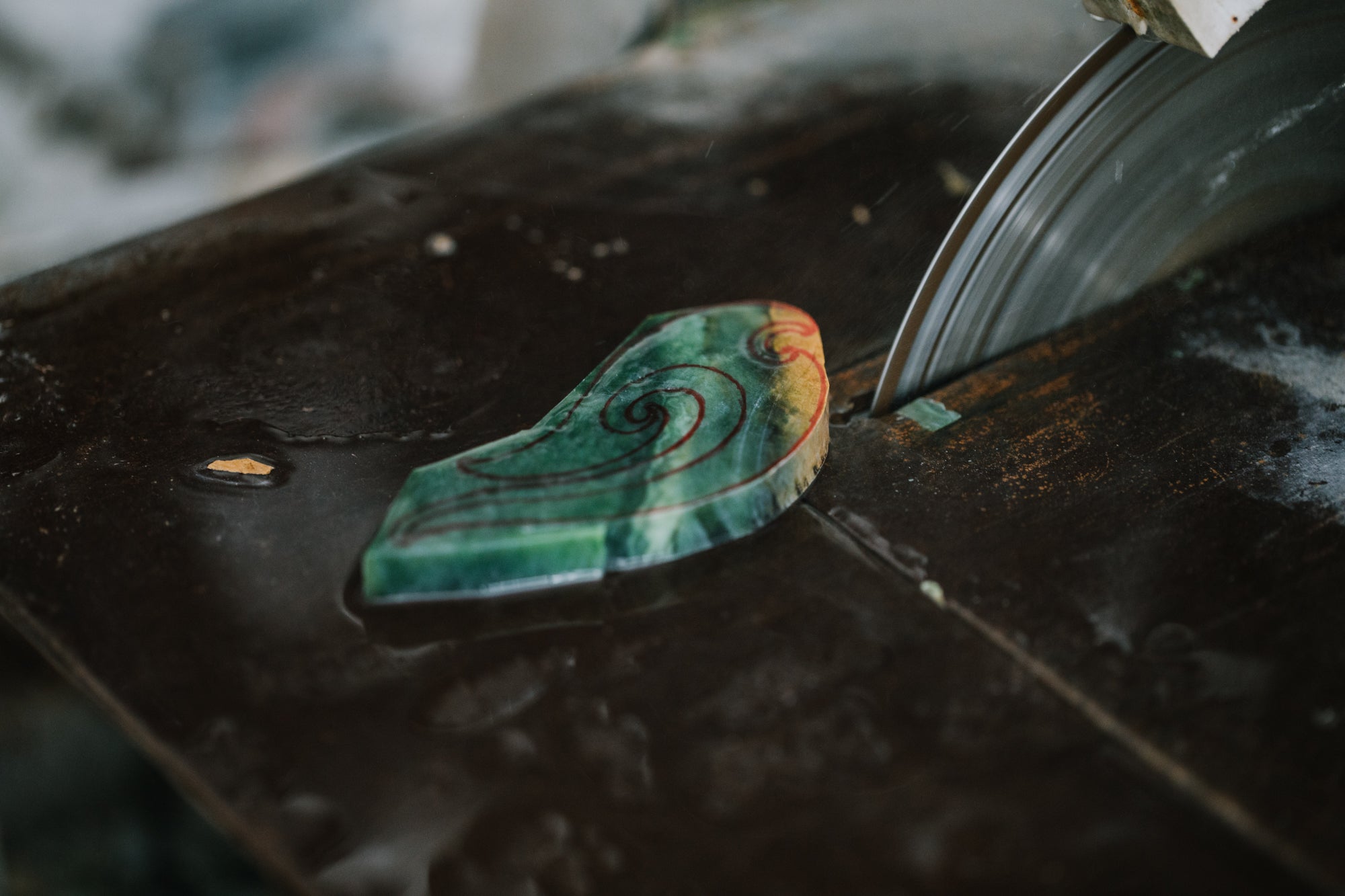
Shaping
Carvers then use the diamond-plated wheels on the grinder to remove the bulk of the stone around the design and begin shaping the piece. Maintaining the flow of the design during grinding requires great skill and experience.
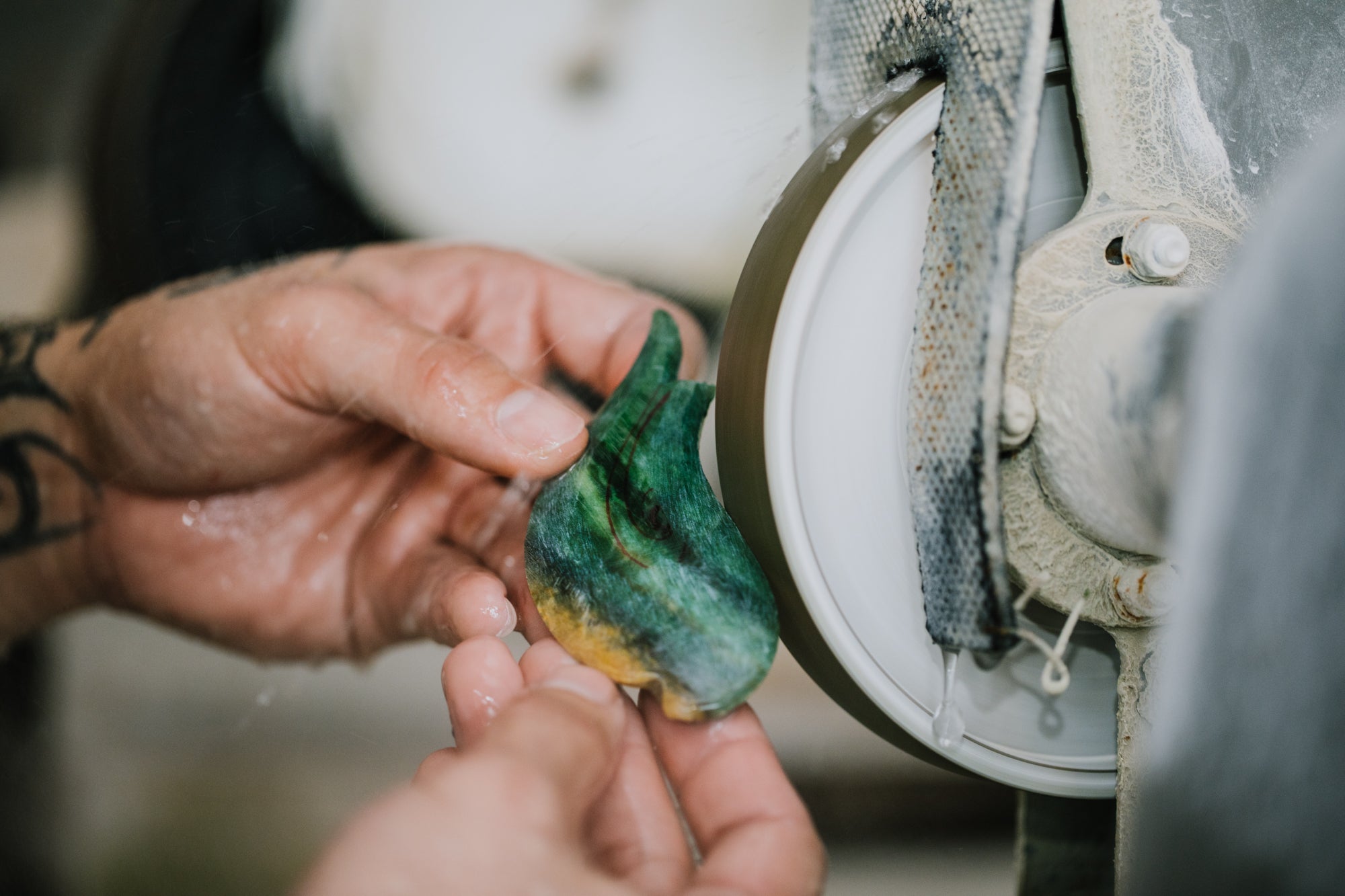
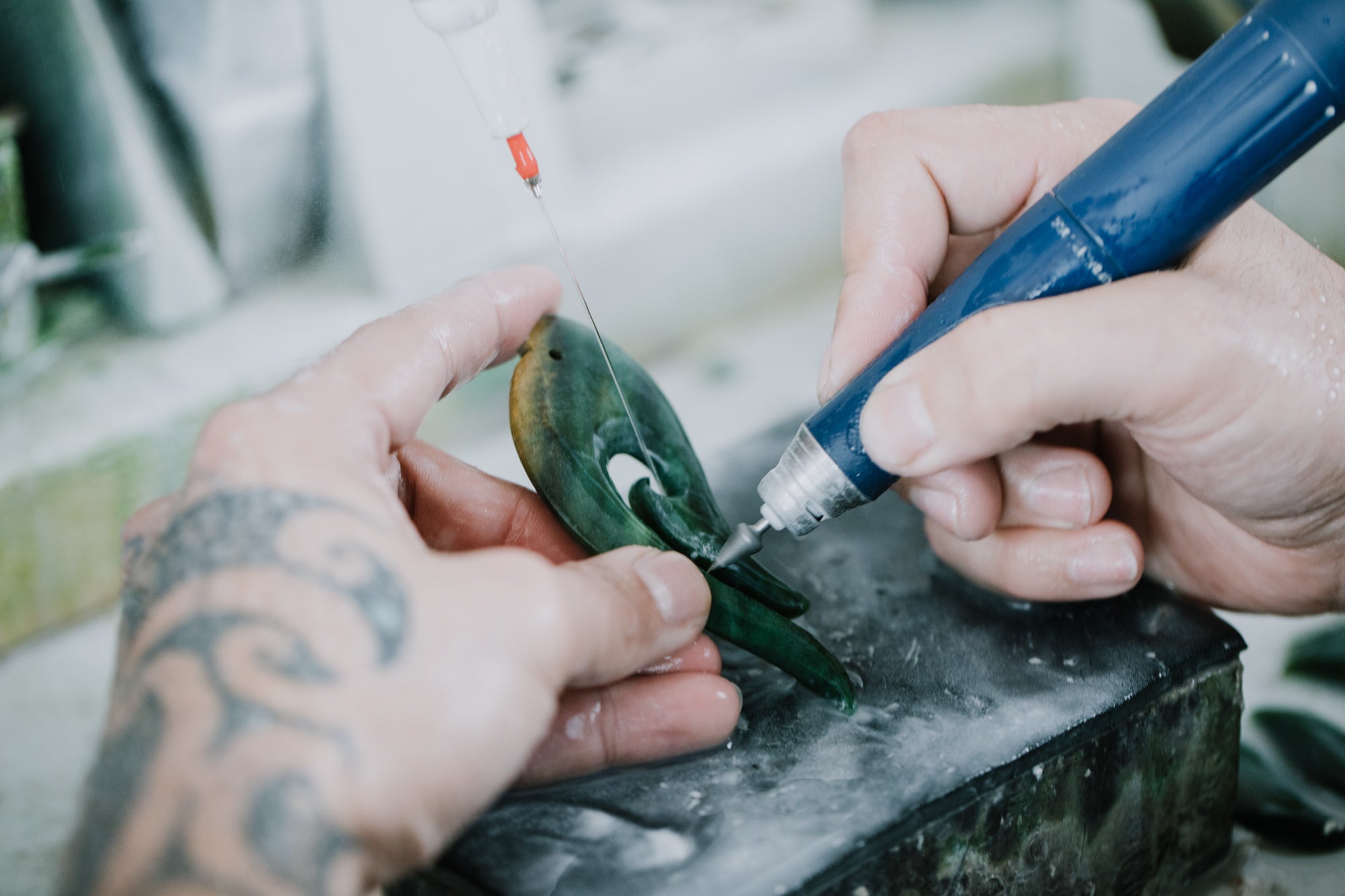
The finer details
Regardless of whether artists are carving a classic design they’ve practiced many times or a new contemporary piece, patience and persistence are imperative. Carvers need to be meticulous, as jade is an unforgiving stone that readily showcases any scratches or nicks. A hand piece with an assortment of diamond-tipped tools is required for an artist to carve the finer, more intricate details, including removing the internal pieces of the stone that the grinder can’t reach.
Finishing the piece
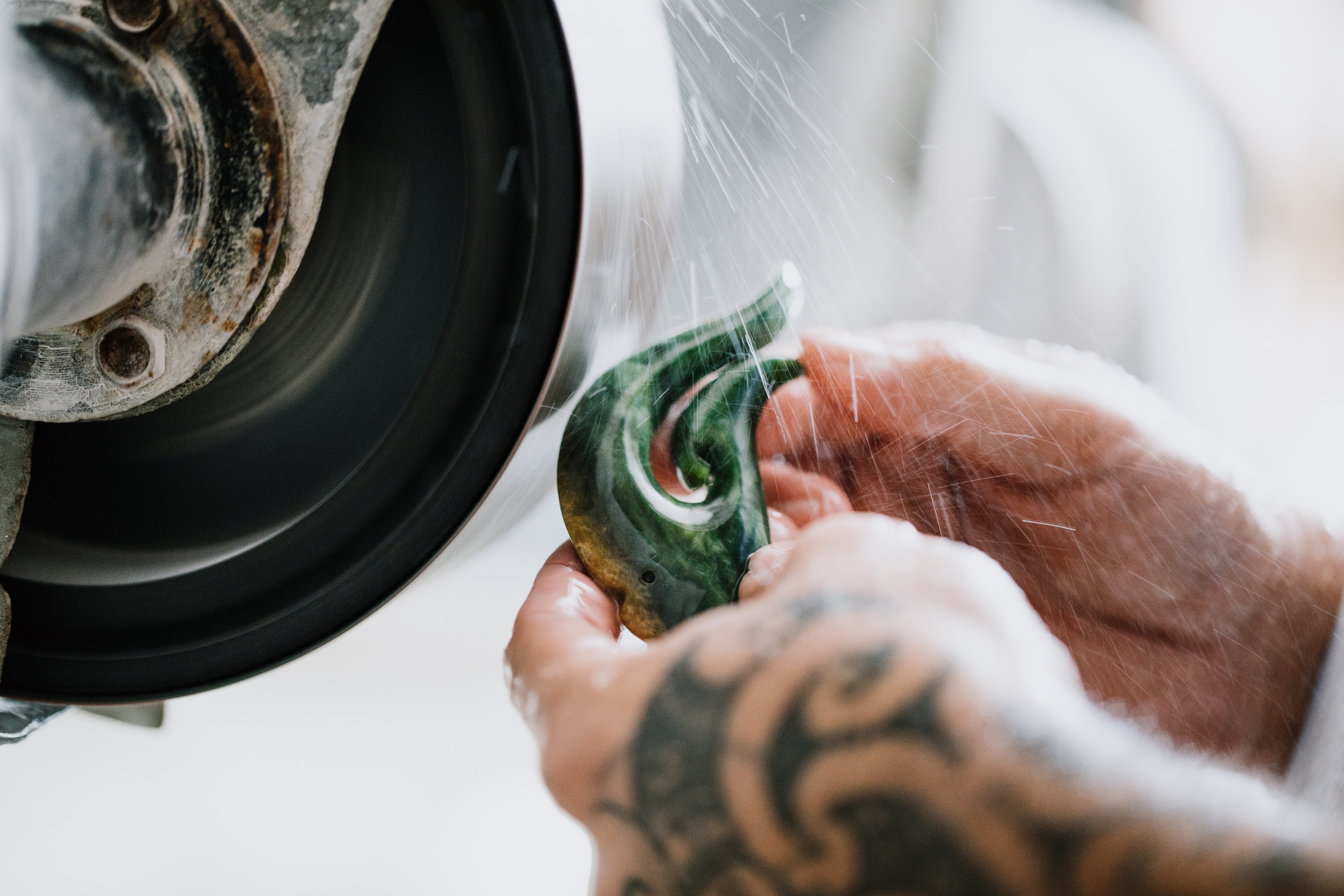
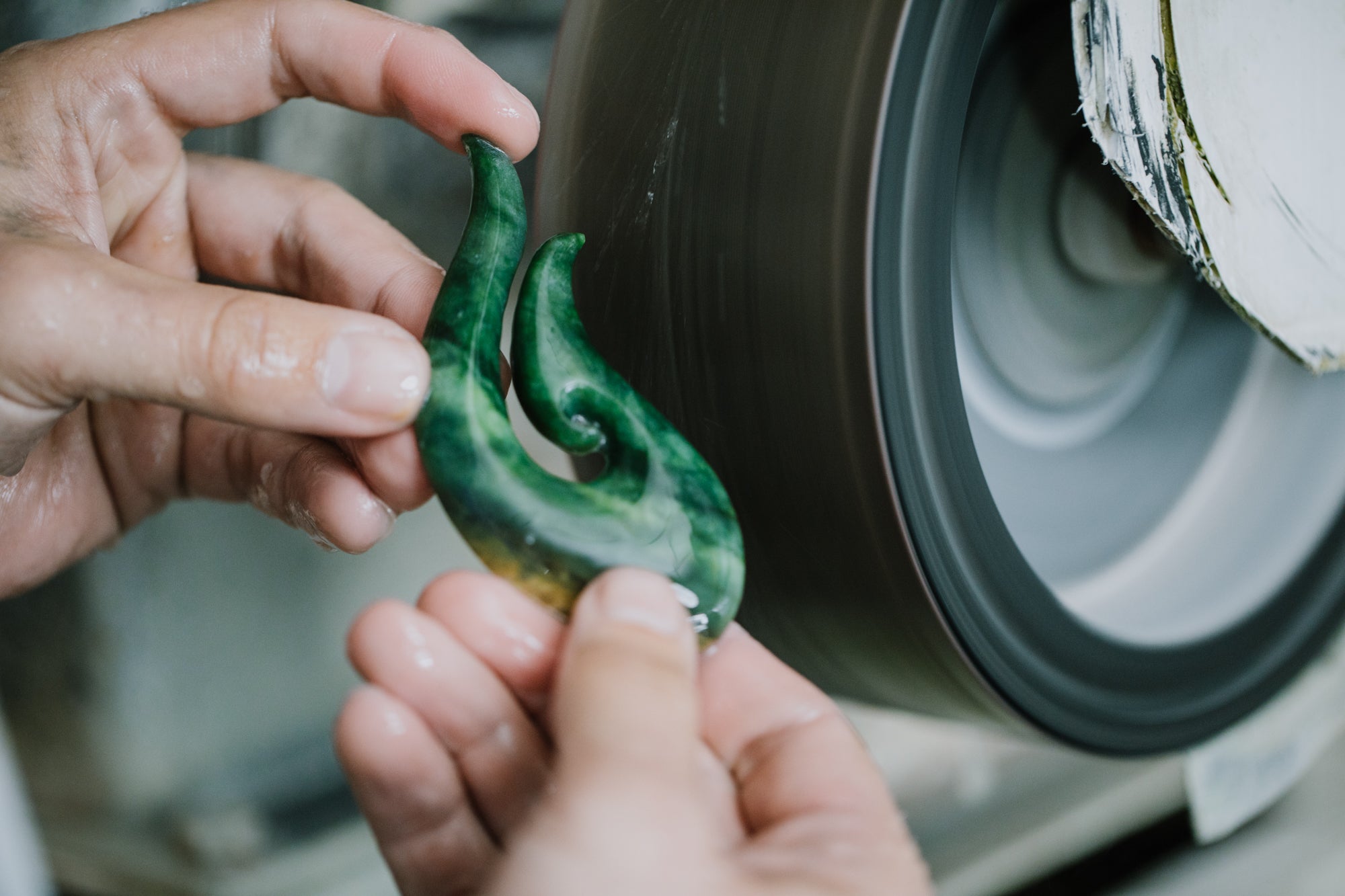
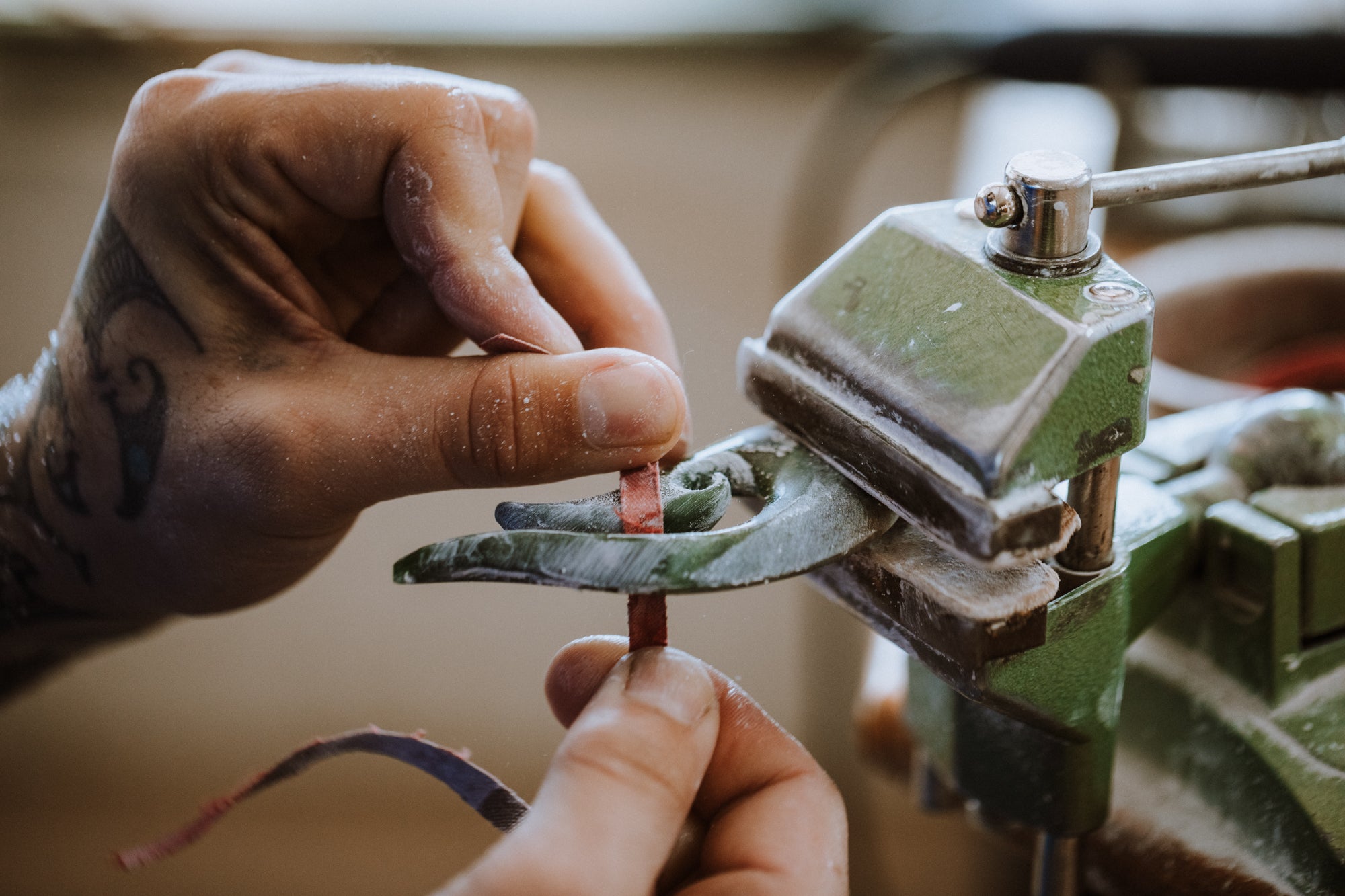
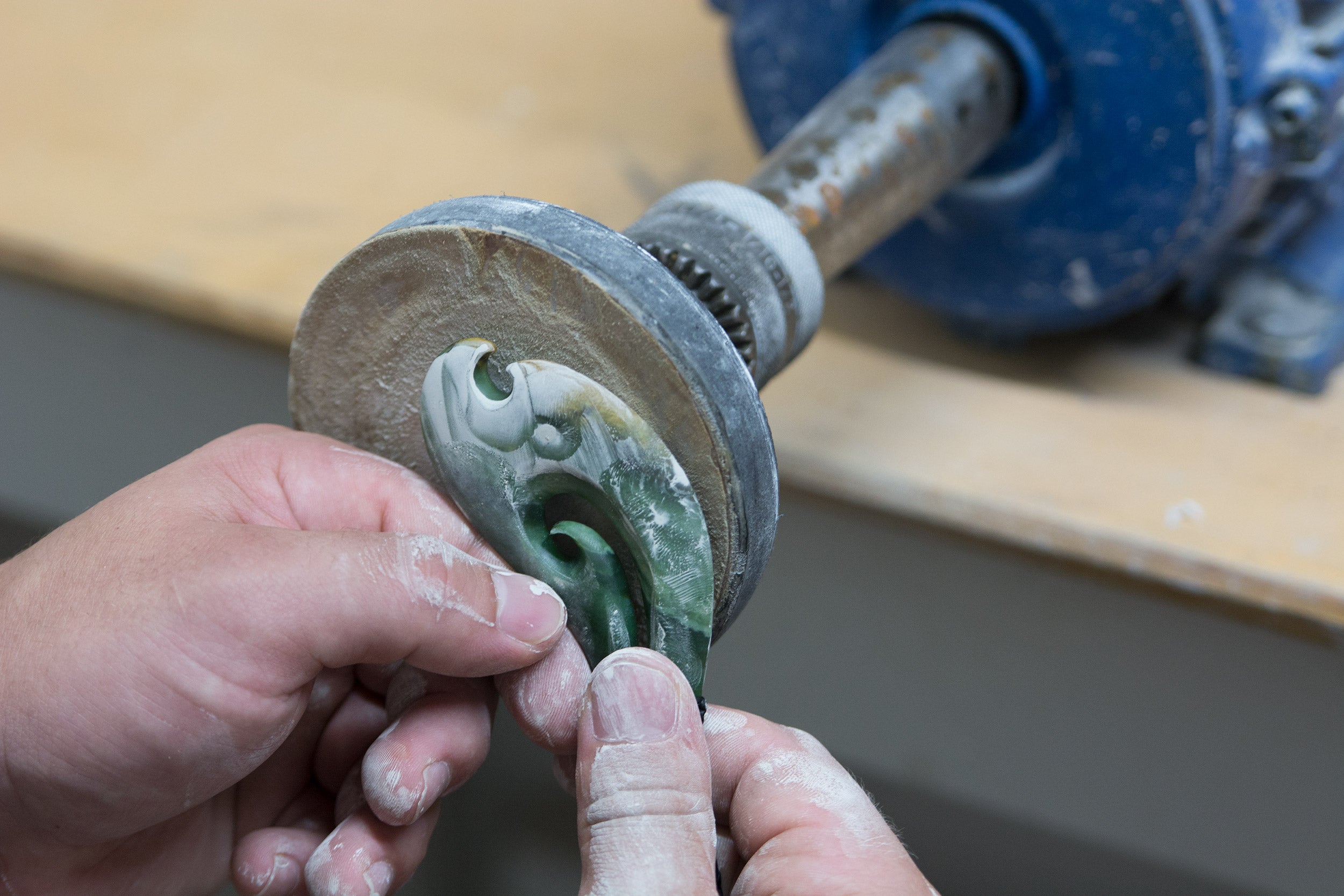
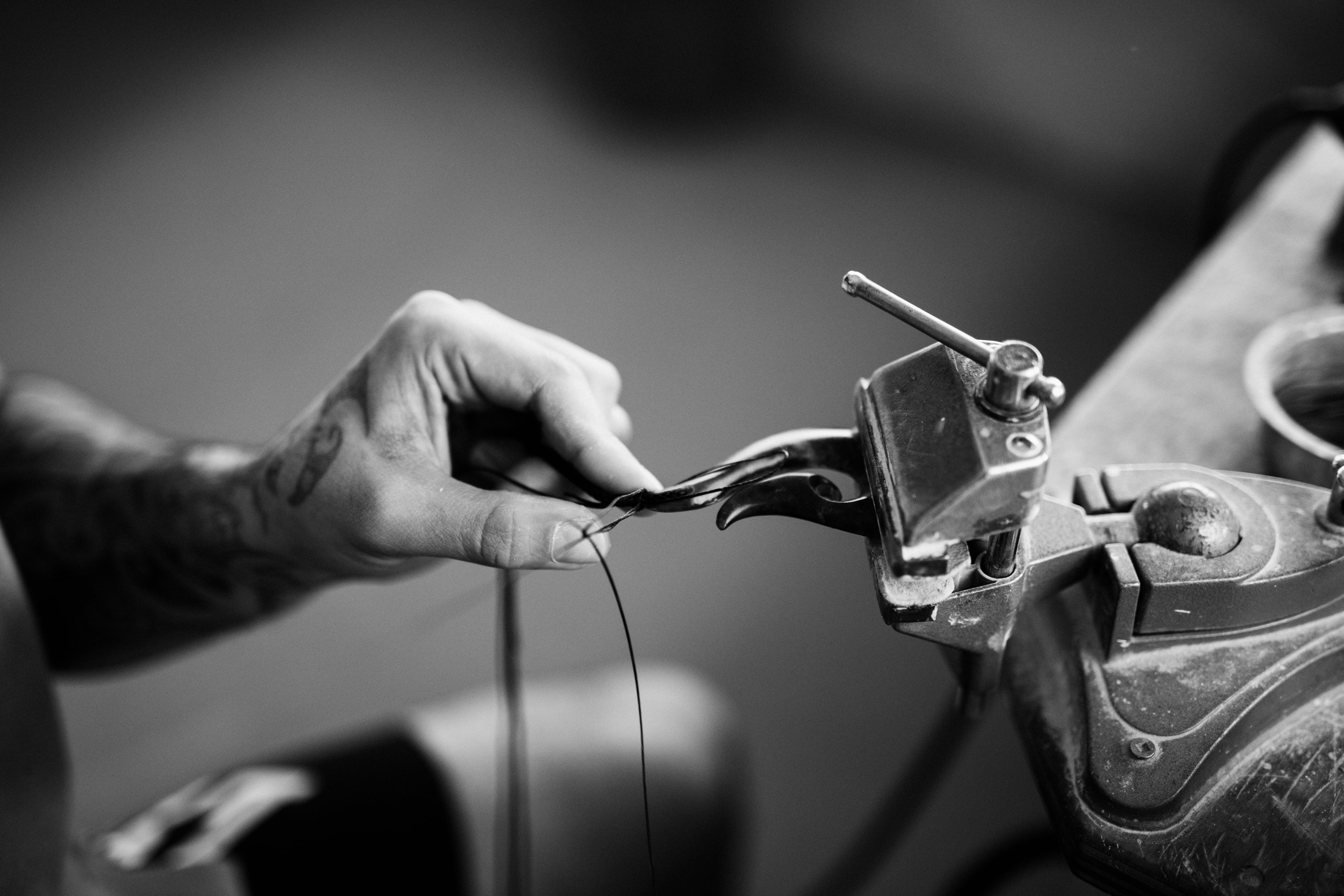
Binding a pendant
There are many different binding techniques an artist can use to join their carving to a cord so it can be worn around the neck. In New Zealand, natural fibres from cabbage trees or flax were traditionally used for binding, but today waxed synthetic cord is most commonly used.
Follow Us
Stay in the know on new releases, special offers, and more.